The Difference Between Vertical Machining Center And Horizontal Machining Center
Horizontal machining center refers to a machining center where the spindle axis is parallel to the worktable, and is mainly suitable for processing box-type parts.
The main shaft of the horizontal machining center is in a horizontal state, usually with a square worktable that can be indexed and rotated. Generally, it has 3 to 5 motion coordinates. The common one is three linear motion coordinates plus one rotary motion coordinate. It can make After the workpiece is clamped once, the processing of the remaining four surfaces except the mounting surface and the top surface is completed, which is most suitable for processing box parts. Generally, it has an indexing table or a CNC conversion table, which can process all sides of the workpiece; also It can perform joint movement of multiple coordinates to process complex spatial surfaces.
Some horizontal machining centers are equipped with an automatic exchange table. While processing the workpiece on the workbench at the working position, the workpiece on the workbench at the loading and unloading position can be loaded and unloaded, thereby greatly reducing the auxiliary time and improving Processing efficiency.
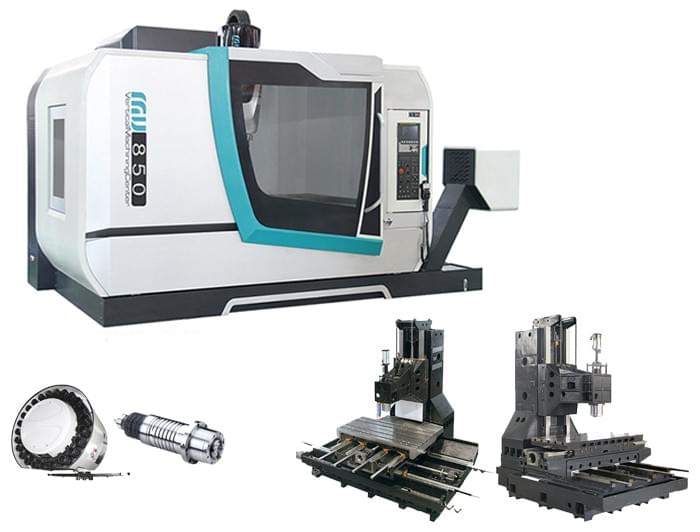
The working principle of the machining center:
After the workpiece is clamped on the machining center once, the digital control system can control the machine tool to automatically select and change tools according to different processing procedures, automatically change the spindle speed, feed speed, and the motion path of the tool relative to the workpiece and other auxiliary functions, in turn Complete multi-process processing on multiple surfaces of the workpiece. And there are a variety of tool change or tool selection functions, so that the production efficiency is greatly improved.
Due to the concentration of processes and automatic tool change, the machining center reduces the time of workpiece clamping, measurement and machine tool adjustment, so that the cutting time of the machine tool reaches about 80% of the machine start time (normal machine tool is only 15-20%); at the same time; It also reduces the turnover, handling and storage time of workpieces between processes, shortens the production cycle, and has obvious economic effects. The machining center is suitable for small and medium batch production with complex parts, high precision requirements, and frequent product replacement.
Compared with the vertical machining center, the horizontal machining center has a complex structure, a large area, and a higher price. Moreover, the horizontal machining center is inconvenient to observe during processing, and it is inconvenient to clamp and measure parts, but it is inconvenient for chip removal during processing. Easy and good for processing.
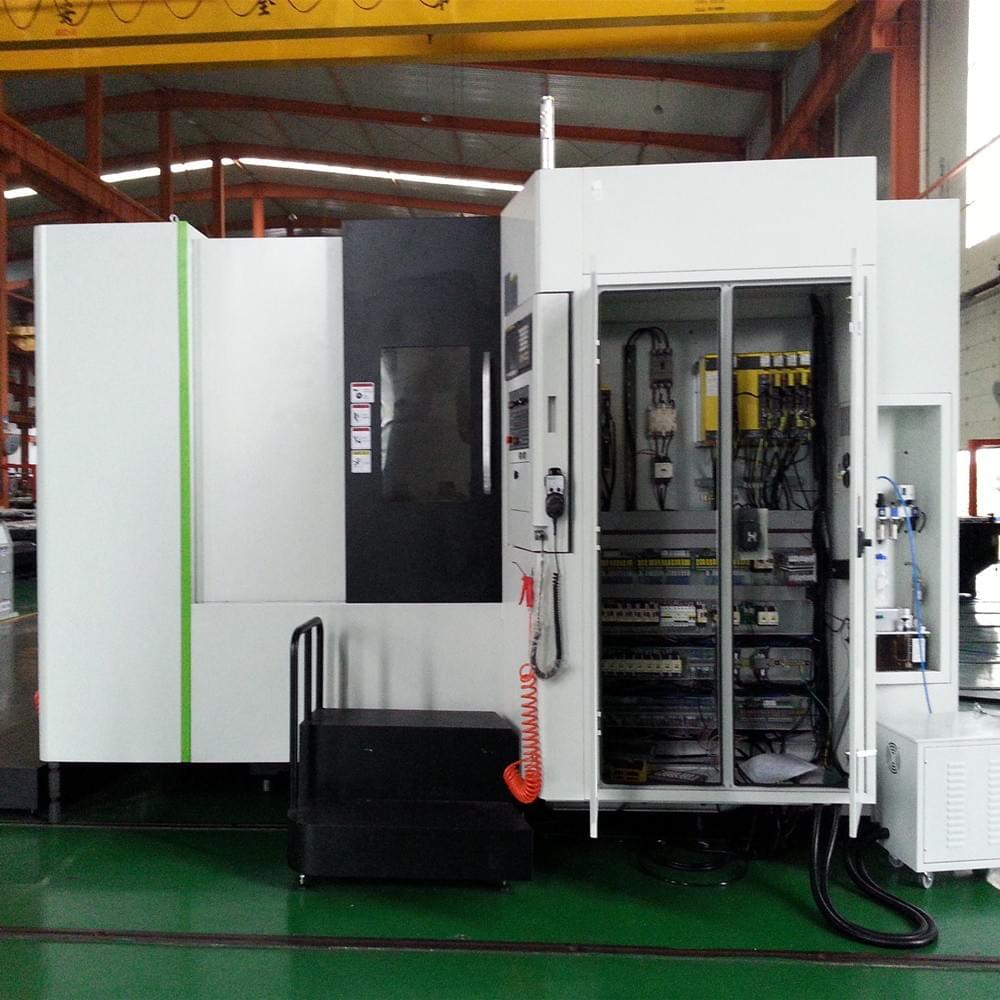
Types and characteristics of horizontal machining centers:
Horizontal machining centers are divided into fixed column type and mobile column type according to whether the column is moving.
(1) Fixed column type
1) The worktable moves in the cross direction, the worktable moves in the X and Z directions, the spindle box moves in the Y direction, and the spindle box has two types of hanging and side hanging on the column. It is suitable for boring and milling of medium-sized complex parts. Processing.
2) The headstock moves in the cross direction, the headstock moves in the X and Z directions, and the worktable moves in the Y direction. It is suitable for boring and milling of small and medium-sized parts.
3) The headstock is hung on the side and the column. The headstock moves in the Y and Z directions. This layout is similar to the planer type horizontal milling and boring machine, and the worktable moves in the X direction. It is suitable for multi-process processing such as boring and milling of medium-sized parts. .
(2) Movable column and type
1) Planer type, the bed is T-shaped, the worktable moves in the X direction on the front bed, and the column moves in the Z direction on the rear bed. The spindle box has two forms of hanging and side hanging on the column, as Y Directional motion. It is suitable for multi-process processing such as boring and milling of medium and large parts, especially parts with larger lengths.
2) Column cross movement type, the column moves in Z, U (parallel to the X direction), the spindle box moves in the Y direction on the column, and the worktable moves in the X direction on the front bed. It is suitable for boring and boring medium-sized complex parts. Multi-process processing such as milling.
3) Spindle ram feed type, the spindle box moves in the Y direction on the column, the spindle ram moves in the Z direction. The column moves in the X direction. The worktable is fixed or equipped with a rotary worktable. It can be equipped with multiple The worktable is suitable for the processing of multiple small and medium-sized parts, and the workpiece loading and unloading and cutting time can be overlapped.
Vertical Machining Center
Machining center (English abbreviation CNC, full name Computerized Numerical Control): It is a highly automated multifunctional CNC machine tool with a tool magazine and automatic tool changer.
After the workpiece is clamped on the machining center once, the digital control system can control the machine tool to automatically select and replace the tools according to different processes, and automatically change the spindle speed, feed, and the motion trajectory of the tool relative to the workpiece and other auxiliary functions. Multi-process processing on several surfaces of the workpiece. And there are multiple tool change or tool selection functions, which greatly improves production efficiency.
Vertical machining center: refers to the machining center with the axis of the spindle and the worktable perpendicular to it. It is mainly suitable for processing complex parts such as plates, disks, molds and small shells. The vertical machining center can complete milling, boring, and drilling. , Tapping and cutting threads. The vertical machining center is at least three-axis two-linkage, and generally can achieve three-axis three-linkage. Some can perform five-axis and six-axis control. The height of the vertical machining center column is limited. The processing range of box-like workpieces should be reduced, which is the shortcoming of the vertical machining center. But the vertical machining center is easy to clamp and locate the workpiece; the cutting tool movement track is easy to observe, the debugging program is convenient to check and measure, and the problem can be found in time, and the machine can be stopped. Processing or modification; cooling conditions are easy to establish, the cutting fluid can directly reach the tool and the processing surface; the three coordinate axes are consistent with the Cartesian coordinate system, and the intuitive feel is consistent with the pattern perspective, and the chips are easy to remove and fall to avoid scratches. Compared with the corresponding horizontal machining center, the structure is simple, the area is small, and the price is lower.