Introduction Of Turning Machining Center?
The turning machining center can process various rotating surfaces, such as inner and outer cylindrical surfaces, inner and outer conical surfaces, threads, grooves, end faces and forming surfaces, etc. The machining accuracy can reach IT8 to IT7, and the surface roughness Ra value is 1.6~0.8. It is commonly used in turning To process parts with a single axis.
Application:
Such as straight shafts and general discs, sleeve parts, etc. If you change the installation position of the workpiece or refit the lathe appropriately, you can also process multi-axis parts (such as crankshafts, eccentric wheels, etc.) or disc cams. In single-piece small batch production, various shafts, discs, sleeves and other parts are mostly processed by horizontal lathes or CNC lathes with wide adaptability; large parts with large diameters and short lengths (length-to-diameter ratio 0.3~0.8) are mostly used Vertical lathe processing.
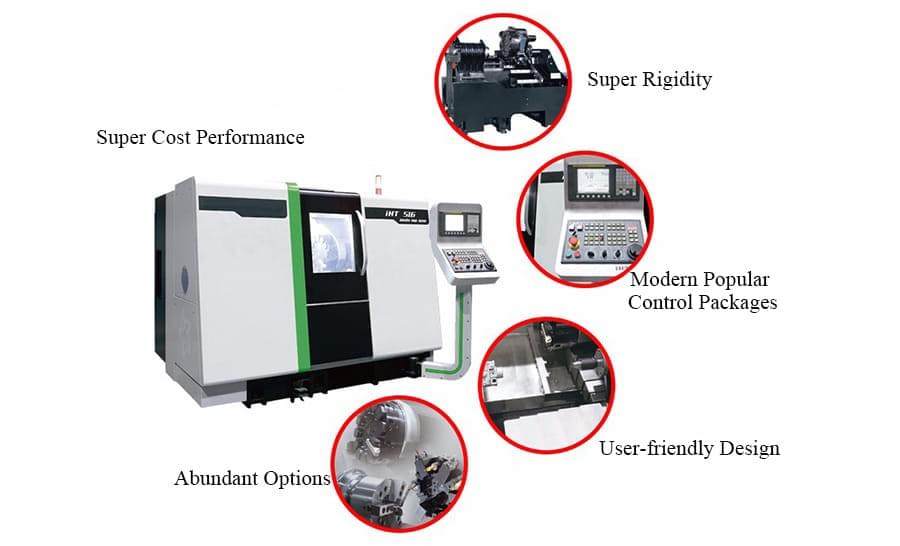
Process Characteristics:
1. It is easy to ensure the position accuracy of each processing surface of the workpiece
a For example, it is easy to ensure the requirements of coaxiality. Use the chuck to install the workpiece, and the rotation axis is the rotation axis of the lathe spindle.
b It is easy to ensure the perpendicularity of the end face to the axis. The verticality of the horizontal slide guide rail and the axis of rotation of the workpiece is required.
2. The cutting process is relatively stable, avoiding inertial force and impact force, allowing the use of larger cutting parameters, high-speed cutting, and improving productivity.
3. Suitable for finishing of non-ferrous metal parts. When the surface roughness of non-ferrous metal parts is large and the Ra value is small, it is not suitable to use grinding processing, and turning or milling is required. High quality can be achieved when using diamond turning tools for fine turning.
4. The tool is simple. The manufacturing, sharpening and installation of turning tools are all convenient.